Creare is advancing the state‑of-the-art in manufacturing. We apply our unique and diverse expertise to develop innovative solutions for our clients’ manufacturing challenges. At Creare, we consistently focus not only on the development of innovative solutions, but their implementation in a real world manufacturing environment. In doing so, Creare provides innovative, yet practical, solutions for our clients that deliver sustainable quality improvements and frequently substantial cost savings. We achieve this objective by working with key partners in industry including prime contractors, materials specialists, component fabricators, machine tool and composite systems companies, as well as tooling suppliers. These key partnerships enable Creare to develop innovative, implementable, advanced manufacturing solutions for U.S. industry to fabricate unique parts for extreme requirements.
In the realm of advanced manufacturing, our expertise and cross‑disciplinary approach to technology development enables us to develop novel solutions to critical problems related to Additive Manufacturing, Machining, Grinding, Composites Fabrication, Non-Contact Measurement, and Inspection.
Creare has extensive experience transitioning advanced manufacturing technologies to large DoD programs in partnership with major defense prime contractors. We have also developed specialized internal fabrication processes for Stamping and Forming that enable us to build unique components and systems to meet our customer’s needs.
Creare is at the forefront of new Additive Manufacturing processes, as we have developed the Additive Friction Stir (AFS) process for component fabrication and repair. Creare’s novel AFS process adapts and miniaturizes conventional solid-state friction stir welding (FSW) using compact, high-speed spindles and consumable tools to facilitate deposition of material for high strength repairs. We have established that our AFS approach reduces torques and thrust forces by orders of magnitude compared to conventional FSW, making compact tools possible for the high-strength repair and reinforcement of aluminum alloys, titanium alloys, and stainless steels. Fundamentally, the AFS results in a high-strength repair due to the refined, equiaxed microstructure and the metallurgical “bond” achieved between the base material and the repair.
At Creare, we conduct applied research at both conventional and ultraprecision scales for machining operations, drawing on our capabilities in heat transfer, structural mechanics, machine design, materials, and computer modeling to develop innovative processes and equipment.
For high-performance machining, we developed unique cutting tool cooling technologies that eliminate the need for conventional flood coolants, while significantly enhancing machining performance. Creare’s cryogenic machining approach uses a very small flow of liquid nitrogen (approximately 1/100 of conventional coolants) delivered through-tool to enable high-speed, environmentally friendly manufacturing while enabling a severalfold increase in tool life and a doubling (or more) of processing speed. Our work in ultraprecision machining focuses on the development of hybrid processing of ceramic mirrors. Lasers can be used to reduce cutting forces, increase material removal rates, and enable the machining of difficult materials like ceramic matrix composites (CMCs). To address the challenges, Creare has developed a novel laser-assisted machining (LAM) system. We have not only developed and demonstrated systems in our laboratories, but we have integrated our systems on commercial machine tools for eventual technology transition to the U.S. industrial base.
“Beating the Heat” – Air Force SBIR video describing Creare’s development of the cryogenic machining process for titanium.
For equivalent strength, significant weight reductions can be achieved for high performance military and commercial systems using polymer matrix, thermosetting composites, and thermoplastic composite materials. Creare had developed a novel Integrated, Laser-Assisted Consolidation System (ILACS™) that has significant advantages over off-the-shelf diode laser systems, infrared lamps, or multi-spectral xenon flashlamps. Our innovation is the first of its kind to offer multi-point, full feedback temperature control. Our ILACS controls the precisely adjusts the incident laser power to control nip-point temperature based on user settings, regardless of laydown speed. For relevant aerospace composite materials, we have demonstrated the ability to increase laydown rates by a factor of 3 or more, a decrease in steering radius by nearly a factor of 10 while exceeding quality metrics, reduced part rework, and decreased system maintenance burden. We are currently working with the Air Force and several prime contractors and FPS suppliers to transition our technology from a hardened prototype to a supplied, supported product.
US Air Force Funds Spirit AeroSystems Composites Research – Spirit recently signed a contract with Creare LLC for the development and integration of an advanced laser heater into Spirit’s new robotic automated fiber placement (AFP) machine. The laser heater was originally developed by Creare under AFRL Small Business Innovative Research (SBIR) funding.
Our work in non-contact metrology complements our innovations in other advanced manufacturing technologies. Our laser scanning system is constructed of low cost components, provides “real-time” measurements, and decreases measurement cycle times. Not only is our system highly accurate, we combine the measurement with the necessary diagnostics so that a quick pass/fail determination about the part can be made. The system can be deployed as a held-held unit or mounted on a robot.
We have successfully demonstrated our scanning technology on the following applications:
- Measuring the diameter and angle of large numbers of laser-drilled holes.
- Scanning of parts, surface contours and fasteners on an aircraft skin.
- Scanning of integrally-bladed rotor disks for gas turbine engines.
By combining our expertise in non-contact measurement, software, as well as systems development and engineering, we develop specialized inspection equipment for our clients. These devices and systems often replace inaccurate, inconsistent, and time-consuming manual measurements, offering substantial gains in inspection fidelity and speed.
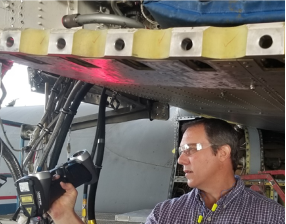
Bolted-bonded wing repair scanning using commercial scanning equipment with Creare custom software. Our software enables the direct fabrication of the wing repair from the initial scan, cutting repair time by more than half. (Creare owned photo)
Creare has developed innovative precision stamping and forming processes, simultaneously applying both creativity and fundamental engineering principles to develop rapid and cost-effective production techniques.
To fabricate high-performance, microchannel heat exchangers, we developed precision forming and blanking processes and equipment, including a compact 1700-ton stamping press. We have fabricated intricate heat exchanger plates from stainless steel, Hastelloy, titanium, and aluminum for a range of geometries and applications. These plates are produced at low cost and include features that enable our heat exchangers to achieve very high thermal effectiveness, minimum weight, high power density, and fault tolerance. Our die designs also incorporate features to promote effective bonding of the plates during fabrication of the complete heat exchanger.
Creare has also developed superplastic compression forming processes for the low-cost production of precision microwave and munitions components. The processes involve the use of hydraulic pressure to force a blank of material on to a die at superplastic temperatures and strain rates.